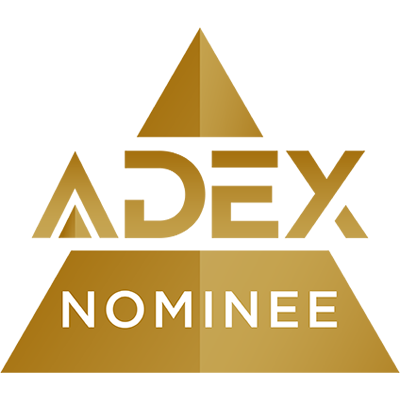
The Design Process
- The main input & starting point for a rainscreen cladding projects is architectural elevations. Cladding design team should work on the cad and determine the grid design and submit to the architects in file for review and confirmation.
- Once architectural details is confirmed, engineering & design for the system starts. As a result, a detailed submission is created with architectural elevations, plans, sections, mechanic and typical details. This will than be used to takeout material and quantities – including but not limited with the panel quantities and fastening elements.
- Cladding system is packed at the cladding designer’s warehouse while panel manufacturer packs the panels – and both is shipped to job site.
- License installer crew will first check the material and make sure every product in the BOQ is received. Than, looking at the shop drawings and building’s plumbness, determine the projection of panels and start installing the façade in accordance with the provided shop drawings.
Sustainability
Rainscreen cladding systems have 2 main advantages.
1. There is a cavity between the finish material and the structural sheeting of the premises, which can be filled with proper type of insulation for increased R value. While conventional cladding systems can accommodate 3” of insulation, S’ystem 2 can be projected enough to create a cavity for 12” thick insulation, providing an R40 insulation value on the walls.
2. Because of the chimney effect, there’s a constant air circulation between the architectural surface ( panel surface) and the structural surface of the premises – or the insulation, resulting in an air circulation with a lot of advantages to the building, like an added R value, minimize condensation on and inside the insulation, preventing bugs nesting inside the cavity.
MAKING DREAM SURFACES ATTAINABLE
MSI is the leading nationwide distributor of flooring, countertop, wall tile, and hardscaping products in North America. Headquartered in Orange, California, MSI maintains over 40 state-of-the-art showrooms and distribution centers across the U.S. and Canada, with domestic manufacturing facilities for Q™ Premium Natural Quartz in Latta, South Carolina, and Premium LVT in Cartersville, Georgia.
Looking ahead, our goal is simple: To contribute to a world where anyone can afford to create a beautiful space to live, work, and play. In support of this goal, we have very ambitious expansion plans, including opening new branches across the U.S. and Canada, as well as continuing to introduce new and innovative products across all major product lines.